Variety and design are key competitive advantages for glass compared to other packaging materials. Apart from product-specific requirements, glass plants face the challenge of integrating an existing mix of equipment with the need to implement new technologies and, on the other hand, limiting financial investment budgets. Supporting the management of this variety intelligently and simply is the clear strategic focus of family-owned company Dr. Günther Inspections, writes Mark Ziegler.
In general, cold end container glass inspection lines consist of three types of machine: a camera inspection machine for the body (sidewall), then a second camera inspection machine for the base/finish, and one at the end of a starwheel machine. Family-owned company Dr. Günther Inspections specialises in the automatic inspection and sorting of container glass, focusing on non-contact camera inspection machines. The German firm’s R&D team has developed a clear concept to differentiate its standard inspection equipment from an advanced version by adding a number of inspection modules, thereby broadening its product portfolio to suit the needs of any glass plant investing in new technology.

CSWI machine
The standard version of Dr. Günther’s camera sidewall inspection machine (CSWI) has six cameras in six positions to detect body defects, planity and dimensions. This configuration is suitable for many customers, especially when articles are more or less in the standard range or the client has a limited budget. Of particular note is the symmetrical camera/light source concept, which uses one light source for each camera position. Consequently, the inspection result is independent from the container orientation. This permits a more precise execution of different detection tasks – with fewer shadows, for example. Detection of the outside contour or the ovality also becomes possible. In addition to the standard configuration CSWI, different modules are available for specific requirements.
Module 1: Shoulder camera and thread + mouth crack inspection
Many customers use the module with shoulder cameras. This allows defects in the neck-, thread- and mouth-area to be picked up with specifically arranged cameras. This module serves also to detect cracks in the mouth area. The 360° thread inspection covers broken or unfilled threads, bubbles and inclusions in or between the thread turn. Automatic seam masking is included, as well as recognition of logos and engravings. For bottles and especially for jars, dip/saddle detection replaces the mechanical vacuum test in the starwheel machine. This camera-based variant is extremely precise up to very high inspection speeds.
Module 2: Stress inspection
Stress in the body of the container can lead to a potentially dangerous collapse. With module 2, using polarised light, glass stress can easily be detected.
Module 3: Low Contrast
Dr. Günther’s R&D team has developed ‘smart lighting’, a special low contrast detection system combining multi-image illumination technology with high-speed algorithms. As a result, very small cosmetic defects can be detected.
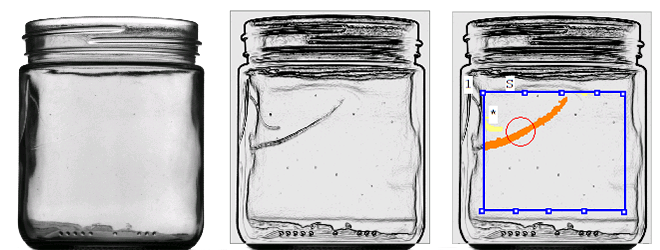
Module 4: Flacons
This module comprises multi-image illumination for premium cosmetics products. Tilo Günther, Head of R&D and Project Management, is proud of this advanced solution package for this sector: “Smart lighting is a key component. For this reason, specific R&D investments have been made by the team. A special image processing module in the software makes even the smallest cosmetic defects visible. Checking washboards and folds of flacons is just as easy as checking for symmetry of the overall shape and the inner bottom contour.” High class flacons must not have cosmetic defects. “The packaging is a fundamental component of the brand perception by the consumer and not only among females,” says his sister Linda, the company’s Commercial Manager, with a smile.
Base and finish inspection machine
The standard set-up of Dr. Günther’s base and finish machine inspects the mouth rim to detect a damaged mouth or open blisters and cracks, and to carry out the so-called LOF (line over finish) test. A special software feature can find defects on or near the mould seam and differentiate between knurling and real defects on or near the knurling.
Module 1: Wirde edge and overpress
Among the most critical defects in glass container production are overpress and wire edge, particularly for narrow neck press and blow (NNPB) producers. An overpress is located on the inner rim of the sealing surface, like a fin of glass extending above the sealing surface. Wire edge is also a fin of glass but it is located under the inner ring of the sealing surface. The reasons for both defects lie in a too-high gob weight or in problems related to the plunger movement. Both defect types can easily be detected by this module, based on the combination of precise cameras and innovative software architecture. Dr. Friedrich Günther, founder of the company, is proud to have been among the first to offer a technology solution for these critical defects in high-speed NNPB productions.
Module 2: Unfilled shoulder
According to Dr. Günther, with one of the company’s self-built light sources, it is possible to inspect the article shoulder from above. “Shape deviations in the shoulder of cream jars, for example, are very hard to detect by standard camera inspections. With our custom-made solution, we have a precise detection for these defect types. The consistently good feedback shows us the high level of functionality in practice.”
Module 3: Mould number reader
The mould number reader can be used regardless of the orientation of the bottle. Dot code and alphanumeric codes can both be read. In this module, the camera is mounted on top of the bottle, with the light source underneath the bottom. In conjunction with the sidewall inspection machine, rejection of defect bottles is guaranteed.
Module 4: Inner bore diameter
Inner bore measurements for containers and ampoules are among the important requirements because the filling nozzle always has to fit precisely into the ampoule. Dr. Günther R&D experts have developed an accurate camera set-up that replaces existing mechanical systems in the starwheel machine. The inspection unit consists of a camera above the bottle and a light source mounted below the bottle. In addition to the inner bore diameter, spikes and ovality problems are also detected.
Module 5: Bottom inspection for flacons
Flacons typically have much higher quality requirements. Special shapes or a different glass structure, such as greater glass thickness, mean that defect detection is significantly more challenging than with standard beer bottles, for example. Further required test criteria concern the measurement of the bottom height, which is important to ensure the break resistance. In addition, image processing of the container bottom, especially bottom notch recognition, is another criterion.
Module 6: Stress in the bottom
This module uses a set-up with polarised light and can detect stress problems in the bottom. Stress in this area is very critical, as it can lead to a large break with big pieces, which can be dangerous for the consumer.
Technologic differentiation
The cornerstone of technologic differentiation is superior optical precision and image processing technology, which can increase the financial performance of a glass plant. Dr Günther’s sidewall machines use one light source per camera position, permitting more opportunities for the detection of different defects. Another important feature is a new machine learning algorithm, combined with a multi-image processing engine. This allows greater precision for different inspection tasks over a wide range of articles. As a result, many of the starwheel machine’s mechanical inspection units can be performed by Dr. Günther’s camera machines, such as checks in the most critical areas, planity and tightness, inner bore diameter, container height or dimension and ovality.
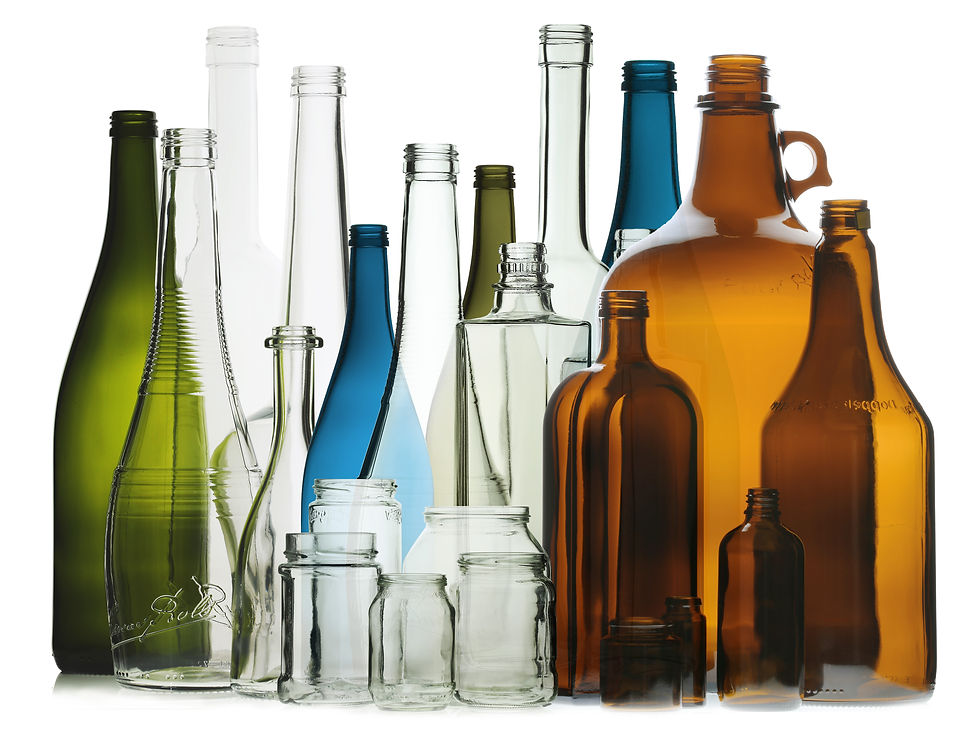
Positive lookout
As an independent, family-owned and run company, Dr. Günther Inspections is well positioned to pursue a long-term development strategy, with the speed and flexibility to fulfil customers’ needs. “What motivates us and gives us selfconfidence is the continuous, positive customer feedback,” states Tilo Günther. “With the combination of our agile service and our flexible approach, we have created good conditions for further growth on a global scale.”
Published in Glass Worldwide January / February 2022
Commentaires